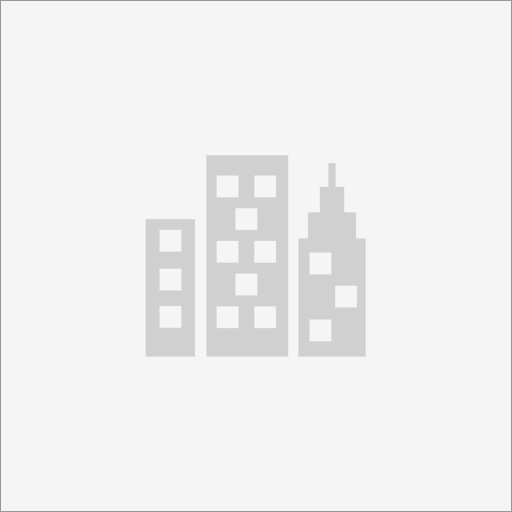
Canadian Nuclear Laboratories
Job title:
Operations Specialist
Company
Canadian Nuclear Laboratories
Job description
The Waste Treatment Center (WTC) is a Class 1 Nuclear Facility built to safely treat low-level radioactive liquid wastes generated at the Chalk River Labs site. This will include treatment of legacy radioactive liquid wastes as part of the Chalk River Labs Environmental Remediation mission.
Operations Specialists (OSs) are important to the facility through ensuring facility systems are fit to operate safely and reliably. To achieve this an OS will be responsible for the development, maintenance, and revision of operating procedures for their respective systems, setting operating parameters and approving system-specific operations for their respective systems. OSs have responsibilities for the safe operation and maintenance of their respective systems.
The OS will be expected to complete a comprehensive training and experience plan, with mentoring and support from an senior Operations Specialist, to become the responsible operation specialist for a facility system (a System Responsible Operations Specialist (SROS) as an appointment by the Facility Manager.
Once trained, an OS will become an operations technical subject matter expert for the design and modification of systems for which they are qualified to support ongoing and future Facility missions
A P.Eng designation can be worked towards through this position.
What you will be doing:
Support for safe and routine Facility operations
· Participate in, and complete the Operations Specialist Training Plan to become a System Responsible Operations Specialist. In support of continuous improvement in training, provide input to Facility training material improvements.
· Learn and gain experience with the design, operational and compliance requirements, and maintenance strategy of an assigned facility system(s). This will involve assisting senior engineers in carrying out technical tasks requiring accuracy in calculations, completeness of data and adherence to prescribed testing, analysis, design or computation methods
· Establishing system maintenance requirements, providing input to the Master Equipment List (MEL), Critical Spare Parts List, and managing ageing and obsolete equipment.
· Provide operations/technical support to the Facility, including: identifying, investigating, and solving operational problems; proposing alternatives/improvements to the existing equipment and/or process to ensure reliable operation of the Facility to meet user needs;
· Technical responsibilities to support facility operation incudes reviewing operational data; preparing Facility reports; marking up master copy of operating flowsheets and supporting condition assessments of process systems
Support for and response to abnormal operating conditions, inadvertent discharges, or administrative or action level exceedances, and any related corrective actions.
· Initiates the appropriate actions including initial investigation and prompt reporting to management. Completes a thorough follow up investigation, troubleshooting and development of a proposed recovery plan.
Recognizes cases where no action should be taken until concurrence is received from the management team. Takes action to implement the recovery plan including revising instructions and ensuring operations staff are trained on any changes
· Identify corrective or remedial actions necessary to prevent events,
Operations staff identify safety concerns and/or opportunities for improvement in system operation.
· Works closely with operations staff to understand the concerns and takes action to address immediate safety concerns.
· Proposes improvements to system operations to improve system safety and operating efficiency.
· Initiates Engineering Change Control and supports the design, installation and commissioning of modifications to the processing system to address concerns raised or opportunities identified. Coordinates implementation of the modifications with the Site maintenance team acting as job supervisor during field work.
Support for General Liquid Waste Branch requirements
· An Operations Specialist may support waste advisors and waste generators in investigating the characteristics of the waste stream based on the specific needs for their facility system, and provides guidance on specific requirements. They may explore innovative ways to receive/store/process waste to meet customer needs while balancing mission priorities.
· Support requirements for executing the Stored Liquid Waste project, including facility upgrades, and equipment operation necessary to pretreat, process, and condition historic liquid waste.
What we are looking for:
Education:
·At minimum, a Bachelors (Honours) in Engineering or Science from a university of recognized standing; or membership in an engineering or scientific professional organization authorized by statute to establish qualification for membership in that organization, or equivalent experience.
Experience:
·1-4 years’ experience in a nuclear operations environment, plant operations/production experience, or water treatment is considered a strong asset.
Abilities and Skills:
Skills, knowledge and experience to include:
· Effective communicate skills (verbally and written) to interact with a variety of groups including management, projects, engineering, and trades support groups to enable safe and reliable operation, to optimize processes, and to support important upgrades or repairs.
· Utilize data processing software (i.e. Excel, Matlab) to trend and analyze data feeds for system performance and operability optimization.
· A strong understanding of fluid-dynamics, chemistry, thermodynamics, basic mechanical physics, and mathematics.
· The ability to quickly learn and understand process systems to develop and maintain operating procedures, operating manuals, and interpret system health data for activities related to their assigned system.
· Critical thinking skills to aid in the interpretation and prioritization of complex information, and separate primary and ancillary issues to identify solutions
· Perform routine and complex field walk downs and investigation.
· Read and understand process flow sheets and schematics
· Demonstrated interpersonal skills, professional conduct, and the ability to excel as a member of a working team that strives to support the overall facility mission to process radioactive liquid waste.
· Strong ability to work in a team environment, interacting with a wide array of personnel from various disciplines.
· Possess the ability to effectively manage their time and coordinate their work to meet established deadlines with minimal supervision.
Security clearance eligibility required: Reliability Status with Site Access Security Clearance (SASC), which has a minimum requirement of 3 years of verifiable history in Canada, Australia, New Zealand, United States and/or the United Kingdom. CNL implements security screening in accordance with the Treasury Board of Canada Secretariat “Standard on Security Screening” and the “Policy on Government Security”.
Why CNL?
Does working with a team across Canada to advance nuclear science and technology for a clean and secure world speak to you? We’re reinventing ourselves to be the pace setters, so we can lead the charge in solving the problems that matter, like building the next generation of clean nuclear and hydrogen energy solutions, developing new and better-targeted cancer treatments, and continuing to lead the world in environmental remediation.
We offer a complete total rewards package:
· paid time off (vacation, sick, floater & personal);
· benefits effective day one, that’s right no waiting period;
· tuition support
· and a pension!
Do Our Priorities Resonate with You?
· Clean energy for today and tomorrow.
· Restore and protect the Environment.
· Contribute to the health of Canadians.
Location:
CNL’s Chalk River laboratory is nestled in the Ottawa Valley and affords our employees an area that is environmentally pristine with extensive forests, hills and numerous small lakes, all of which support a variety of wildlife typical to the southern edge of the Canadian Shield. Many surrounding towns, such as Pembroke, Petawawa and Deep River provide you with unparalleled outdoor adventures at your doorstep! In fact, Deep River was named as the fourth best place to live in Canada in a recent ranking by movingwaldo.com.
CNL is committed to providing an atmosphere free from barriers that promotes equity, diversity and inclusion in achieving our mission. CNL welcomes and celebrates employees, stakeholders and partners of all racial, cultural, and ethnic identities.
CNL also supports a workplace environment and a corporate culture that is built on our Core Values: Respect, Teamwork, Accountability, Safety, Integrity and Excellence which encourage equitable employment practices and career prospects inclusive of accommodations for all employees.
CNL is committed to being an equal-opportunity employer. If you require accommodation measures during any phase of the hiring process, please indicate via our ATS when applying. All information received in relation to accommodation requests will be kept confidential.
The Chalk River Laboratories site is located on the unceded and unsurrendered territory of the Algonquin Anishinaabe people. As an organization, CNL recognizes and appreciates their historic connection to this place. CNL also recognizes the contributions that First Nations, Métis, Inuit and other Indigenous Peoples have made, both in shaping and strengthening this community in particular, and this province and country as a whole.
Expected salary
Location
Chalk River, ON
Job date
Thu, 09 Nov 2023 01:39:51 GMT
To help us track our recruitment effort, please indicate in your email/cover letter where (un-jobs.net) you saw this job posting.