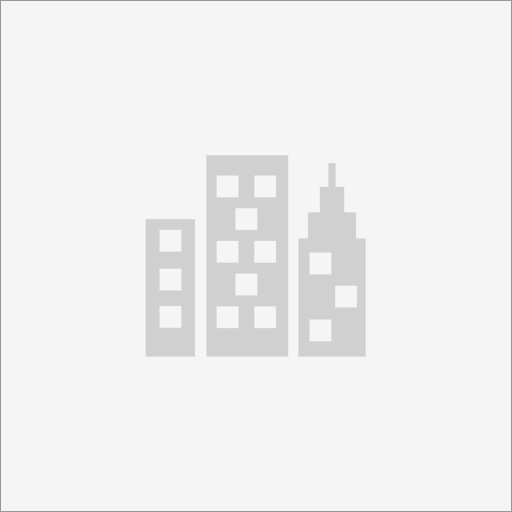
MGS
Job title:
Quality and EHS Manager
Company
MGS
Job description
JOB PURPOSE:As a member of the Site Leadership Team, the Quality and EHS manager will manage and develop the Quality Department and Quality Management System to ensure that plant goals and objectives are achieved, and both product and process meet specification, statutory obligations and customer requirements. The Quality and EHS manager will also be a leader in the development, deployment and continuous improvement of programs and systems that support environmental, health and safety excellence across the MGS Ireland plant.Quality:Develop and implement a comprehensive Quality Strategy for the plant, ensuring all areas/functions are fully engaged in its execution.Manage the day-to-day quality activities of the plant, establishing and monitoring overall plant performance for quality standards using appropriate metrics.Recommend enhancements to the Quality Management System and lead continuous improvement efforts towards better results and reduced costs by embedding quality tools and risk management processes within the system.Develop and manage the Quality and Metrology Engineering team with particular focus on customer needs, compliance, product quality, and risk mitigation.Support the training and development of all staff in relation to quality standards.Play a key leadership role in the areas of Quality Systems Regulations and ISO standards and compliance by constantly promoting awareness of best industry practices, making appropriate decisions on a daily basis through the Quality Department and acting as the final arbitrator on critical quality decisions.Develop, direct and execute project plans from a quality perspective.Compile and analyse operational, test and validation data to establish technical specifications and performance standards for newly designed or modified products and processes.Liaise with customers, identify their quality requirement, and manage any customer complaints.Prepare for audits (both internal and external) and support resolution of audit issues.Oversee preparation of operational schedules to ensure quality of products meets specifications.Review and approve final project development deliverables and results meet customer and QMS requirements.Review, approve, and provide feedback for Quality related decisions for Material Review Board (MRB) as needed.Review, approve, and provide feedback on calibration exception reports.Review, approve, and provide feedback for Non-Conforming Material root-cause analysis, corrective action plans, and completion.Review, approve, and provide feedback for Corrective Action/Preventive Action (CAPA) responses.Quality representative for the authorization of Return Material requestsEHS:Know and follow all of the Company’s safety rules, such as safe work practices and standard operating procedures.Serve as a good role model to employees for safe work practices and behavior by conducting yourself professionally, keeping in mind your own safety and the safety of others.Learn and master all necessary areas of the quality system.Advise and assist the Senior Management Team and other persons involved in planning, organizing, controlling and maintaining a safe and healthy work environment in the plant.Help maintain and continuously improve EHS in the plant by ensuring policies, procedures and processes comply with legislation, promote best practices and align with MGS Mfg. Group’s global EHS Management Program, including risk assessment and management, continuous improvement, EHS training, etc.Proactively coordinate and execute the necessary risk reduction techniques associated with the plant’s operations, and work with colleagues to avoid or reduce those risks and ensure safe systems of work for all activities.Oversee the plant’s emergency management procedures, conduct audits, training, etc, as appropriate to ensure adequate response capabilities.Play a lead role in setting, monitoring and presenting EHS metrics.Carry out investigations into any accidents and near-miss incidents that may occur; record and report on findings as required; notify management of all matters reportable under the appropriate internal and external reporting systems.Review and analyze reports of accidents and near-miss occurrences to make recommendations that help prevent reoccurrences. Identify, implement and monitor the effectiveness of any corrective / preventative actions that may be taken to prevent reoccurrence.Build relationships with key stakeholders to foster support for EHS processes and programs.Oversee the EHS team to promote safe manufacturing practices, procedures, and proper use of equipment and facilities, responding appropriately to any concerns raised by team members in relation to EHS in the plant.Coordinate, prepare and deliver EHS training for employees; both internal and external as required.Support Global EHS initiatives by participating and leading action plan generation and monitoring of EHS related projects.Integrate and partner with the EHS team to promote a proactive safety culture focused on incident prevention, risk reduction and regulatory compliance.Develop specific EHS objectives and create action plans to meet those objectives.Maintain, review and report EHS performance, identifying opportunities for improvement along with implementing preventative and corrective actions as required.Conduct internal EHS audits to ensure regulatory compliance.Monitor, track and lead the functionality of the Safety Suggestion Program.Support multiple site and corporate safety activities as required.Any other duties as assigned.People Management:Provide mentorship and guidance for development of employees by identifying career advancement opportunities and growth within the organization.Manage, coach, and develop a high performing team that meets agreed objectives, and which delivers best practice results, added value and continuous improvements.Set department objectives/KPI’s and review and assess ongoing performance of direct reports.Sets clear expectations for individual/team behaviours.Delegates appropriate tasks to the team, follows up on assigned tasks, responds to training needs of the team, and assists others so that goals are reached.Coordinates and handles any training requirements per the quality system to ensure it is completed timely.Advises team of important information.Evaluate team to identify any skill gaps and develop plans to address any gaps identified.Provide timely feedback about performance strengths and development needs.Supports the performance evaluation process ensuring performance evaluation are completed accurately, timely, and effectively setting SMART goals that contribute to the goals of the overall plant and department and holding employees accountable to the goals set.Ensure organizational sustainability by building and developing a “bench” of internal talent.Participate in the hire, evaluation, and selection of candidates for your team following the New Hire Requisition and interview process working with Human Resources.Holds employees accountable to the Company’s overall policies and procedure, job requirements, and MGS’s Core values and when needed, complete and process Performance Incident Reports or Performance Improvement Plans in conjunction with Human Resources.Observes, communicates, enforces, and leads by example for all Company policies, procedures, and safety regulations. Ensure that MGS’s Core Values remains your team’s highest priority.Effective communication and coordination with Human Resource Department in regard to payroll, time and attendance, and employee relations.Builds teams that represent diversity of values, opinions, and experienceStrong communicator with ability to negotiate internally with stakeholders and with customer with customers and regulatory bodies.Education and Experience:BSc or higher in Quality Management, Engineering, or related science/technical field; MS in a related field would be an advantage.Bachelor’s degree from an accredited college or university with a major in occupational safety, environmental science or a closely related fieldMinimum of 10 years’ experience in a manufacturing environment (MedTech preferred) with 5+ years prior experience in a managerial capacity and 5+ years of relevant EHS experiencePrior experience with new product introduction, validation, Pre-Approval Inspections, and launch activities is desired. Thorough knowledge of cGMPs and cGLPs; current knowledge and/or experience with QA systems such as change control, investigations (manufacturing / laboratory), deviations, CAPA, document management systems, etc.Experience building up a quality culture and quality management capabilities. Specific knowledge of the core quality concepts (e.g. QRM, MRB), skills (e.g. product release, inspection readiness, quality engineering) and infrastructure (e.g. quality systems IT design and integration).Strong critical thinking, relationship building and leadership skills to effectively influence stakeholders at all levels and meet project requirements.Able to effectively prioritize and manage a diversified workload, often to strict deadlines.Strong project management, interpersonal, negotiation, documentation and problem-solving skills.Able to initiate change, improvement, cost reduction and deliver results.Strong commercial approach in all aspects of the operation optimising sales and profit in both short and long term.Strong aptitude for organization, prioritization and managing multiple tasks at the same time.Ability to actively participate in team-oriented processes influence team engagement and to drive team decision making to conclusions / solutions.Must possess a theoretical and practical knowledge of all state and federal regulatory standards.Knowledge of current safety and loss control practices is essential.MGS is an equal opportunities employer
Expected salary
Location
Leixlip, Co Kildare
Job date
Sun, 31 Mar 2024 00:27:32 GMT
To help us track our recruitment effort, please indicate in your email/cover letter where (un-jobs.net) you saw this job posting.